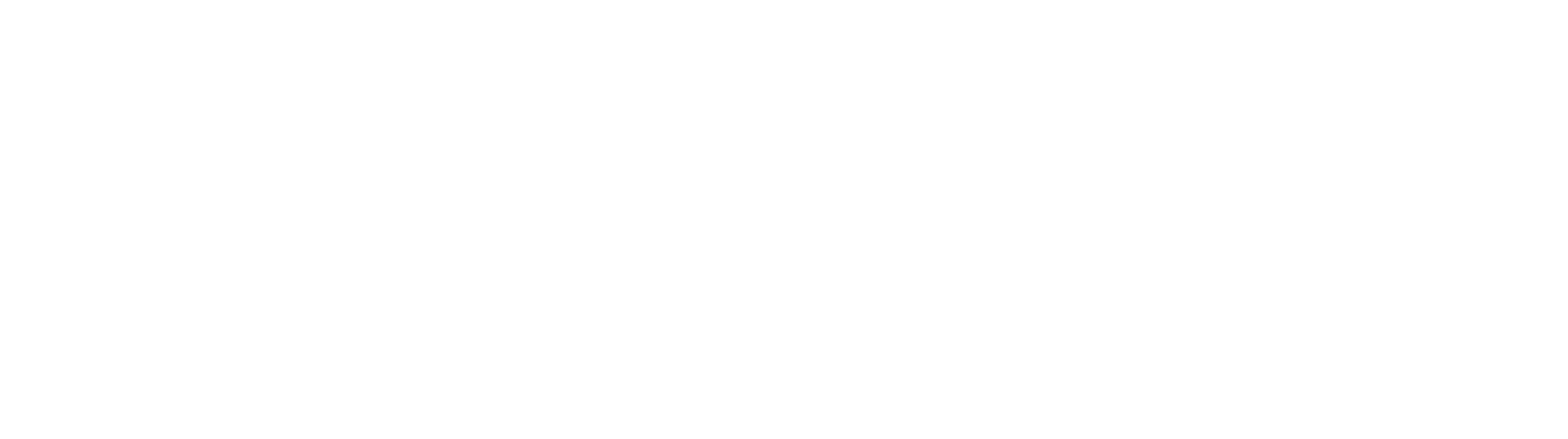
RESURGAM
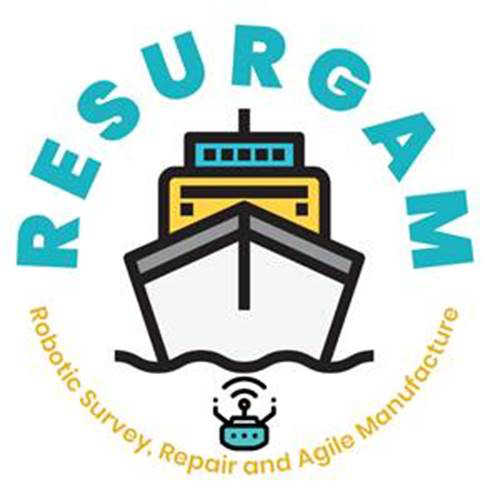
- Title
-
Robotic Survey, Repair and Agile Manufacture (RESURGAM)
- Start Date
-
February 2021
- End Date
-
January 2023
- Funding Body
-
H2020 (MG-3-7-2020 - Improved Production and Maintenance Processes in Shipyards)
- Coordinator
-
Bernardo Hourmat, European Federation for Welding Joining and Cutting (EWF), Belgium
- Project Partners
-
Technische Universiteit Delft, Twi Limited, University Of Lancaster, Element Six Limited, Turkiye Gemi Insa Sanayicileri Birligi Derneg, Engitec Systems International Limited, Aislamientos Termicos De Galicia Sa, Stirweld, Forth Engineering (Cumbria) Ltd, Asociacion Cluster Del Naval Gallego, Ned-Project Sp Z Oo, University of Limerick
- Principal Investigators
-
Daniel Toal, University of Limerick, CRIS
- Research Area
- Website
Introduction
Many of the challenges faced by small and medium-sized EU shipyards can be addressed by improving their productivity for fabricating new, high technology vessels and increasing their access to the specialist repair and maintenance market.
Friction Stir Welding (FSW) is high integrity, low distortion, environmentally benign, welding technique previously investigated in FP7 project HILDA (High Integrity Low Distortion Assembly) and recommended for shipbuilding due to its high quality and suitability for automation. A recent break-through in the tooling material available for FSW now shows potential to enable this process for welding of steel structures (traditionally, it has only been possible to use FSW in aluminium) – this represents a huge opportunity to improve the productivity of European shipyards.
These fabrication and repair capabilities, backed by the secure, digital Industry 4.0 infrastructure and techniques already in widespread use in the automotive and aerospace industries, will facilitate the rapid, coordinated but distributed modular manufacture of ships and watercraft throughout Europe.
Practically, this will allow ships damaged anywhere in the world will have the option of being repaired in place without the need to travel to the nearest dry dock. This will allow ship owners to choose the most suitable yards to conduct their repairs rather than the nearest, and the repairs may be undertaken by yards with no dry dock of their own, thus significantly increasing the number of yards able to undertake such work. All of this will implemented by the European shipyards and Naval architects in Europe.
Aim
In RESURGAM, will combine FSW with the new tool material to deliver:
- The introduction of low-cost friction stir welding (FSW) systems for steel that can be retrofitted to their existing CNC machines;
- The introduction of AI-enabled, robotic FSW systems capable of making underwater weld repairs.
Work Packages
WP1. Marinisation of FSW for steel – transfer the technique of friction stir welding into the maritime sector for the repair and fabrication of steel structures.
WP2. Industry 4.0 Backbone – identify and develop the key I 4.0 technologies and techniques required to enable both remote robotic repair and distributed modular construction concepts.
WP3. Remote underwater repair – develop the concept and prototype hardware required to enable the remote, underwater, robotic FSW system.
WP4. Modular Build – develop the concept and prototype hardware required to facilitate the distributed modular construction of ship sub-assemblies along with the digital infrastructure to support the exchange of data between the designers, builders, supply chain and classification societies.
WP5. Integration and Demonstration – brings together the hardware and software developments undertaken in WP1 to WP4, integrating them into a functional whole and demonstrating that this delivers the results.
WP6. Dissemination, Communication and Exploitation of Results – current dissemination and communication policy to ensure that relevant, accurate, and consistent information reach the target stakeholders and audiences
WP7 Coordination and Project Management – overall project coordination, ensuring contractual obligations and administrative management
Contact
Daniel Toal, UL, CRIS
Email – ei.lu@laoT.leinaD